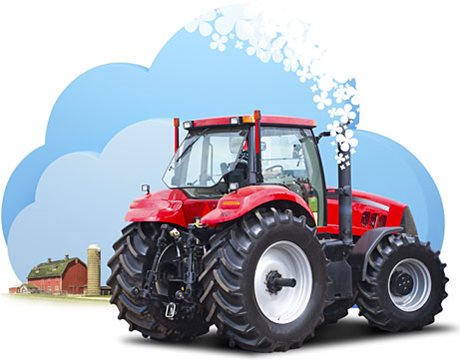
Farm air will be cleaner this year. As the U.S. Environmental Protection Agency’s deadline for zero emissions for “nonroad” diesel vehicles approaches, many farm equipment manufactures are rolling out their solutions. Called Tier 4 Final, this stage in emissions reductions marks the end of a long multi-tiered road, with near-zero emissions for farm vehicles the final destination. The success of the many new engines on the market is a testament to the creativity, ingenuity, and diversity of engineering today.
Back in 1996 when the EPA told truck and auto manufactures they must cut emissions, John Deere, Caterpillar, and Cummins may have seen the writing on the wall but they didn’t have too much to worry about at that moment. Their bread and butter machinery was not meant for the highway. But in 2006, things changed. Tractors, combines, excavators, and other heavy-duty diesel vehicles would have to cut their emissions of nitrogen oxides and particulate matter by 90% (depending on the horsepower) by 2011 and then down to nearly nothing by 2014.
Bringing emissions down to near zero is a unique challenge for diesel engines. Without an after exhaust-treatment system, it’s impossible to cut both nitrogen oxides as waste. Burn up all the particle matter and you increase the nitrogen oxide output. Reticulate the exhaust and the particulate matter levels go up. Understanding the difficulty of the problem, the EPA eased the law in with tiers over the years.
The final Tier 4 engines that are hitting the field this summer have made the big jump down with a handful of solutions, and, in some cases, some positive side effects.
Meeting the Standard
The technology for cutting emissions fell into two camps. On the one hand are engines that take the exhaust and bring it back into the engine, to cool it and reduce the nitrogen oxides. These exhaust gas recirculation (EGR) engines require a particle filter as well. This was the method used by John Deere up to 2011.
![]() |
The Case IH traktor Puma 195 CVX is one of the machines with Tier 4 compliant engines. Image: Wikimedia Commons |
Another solution is the selective catalytic reduction (SCR): Burn up all the particulate matter in the engine and then deal with the nitrogen oxides post combustion by passing it through a catalyst.
The latter is the solution used by Case IH(and John Deere tacked an SCR on to their EGR to meet the final Tier 4 regulations). “For us it was how do we get there, how do we meet the standard and give simplicity back to customers,” says Leo Bose, Case IH’s commercial training manager. “Burning up the particle matter came with an advantage: You’ve increased the energy output, with a 10% savings on fuel.”
To the farmer, this means the higher cost of the machinery could be outweighed by the fuel savings and extra power. “Our engineers said that when the customer puts fuel in that tractor, we want to make sure he uses it all for power,” says Bose. “We’ve tuned that engine for power, taking all that particulate matter and burned it up for power. But it’s a double-edged sword. If you’re burning it up, the nitrogen oxide gets higher.”
Quieter Engines
The other side of that blade is dulled with diesel exhaust fluid, or AdBlue as the company calls it. It is shot into the exhaust as it passes through a honeycomb catalyst chamber, breaking the nitrogen oxide into a simpler, safer form: nitrogen and water.
“That’s all that the SCR chamber does with the diesel exhaust fluid,” says Bose. The fluid costs less than the fuel and the catalyst never needs maintenance. In addition to the added power that comes with the newly cleaned exhaust, there’s another happy byproduct: the engines are quieter. “The customers are enamored of the noise levels,” says Bose.
“Just give me a simple solution that makes it easy for the customer and you’ve got a home run.”
0 comments:
Post a Comment