Hydrogen-powered fuel cells are regarded as the cleanest alternative to the internal combustion engine. After all, the only byproduct they create is water, a substance upon which all life depends. Mass production of fuel cell-powered vehicles would have a huge positive impact on reducing greenhouse gases and cleaning up the atmosphere. The biggest drawback, however, is price. Thanks largely to the use of platinum in fuel cells, these vehicles are too expensive to manufacture.
This may not be the case too much longer. An explosion of research is leading scientists to develop platinum replacements that are improving the efficiency and reducing the cost of fuel-cell systems, without relying on this high-priced and toxic metal.
The most common fuel cell is the Polymer Electrolyte Membrane Fuel Cell (PEMFC) (also known as proton exchange membrane fuel cell). It operates at low temperatures in the 60-150° C range and is well-suited for automotive applications and small-scale distributed generation.
Low-temperature cells such as PEMFC have the highest power density, require high-purity hydrogen, allow for quick start-up, and handle dynamics efficiently, making them ideal for transportation applications and as back-up power generators. A major drawback, however, is that “these fuel cells commonly utilize a noble metal as a catalyst and their performance remains susceptible to both air and fuel impurities,” stated Prabhakar Singh, director for the Center for Clean Energy Engineering at the University of Connecticut, Storrs.
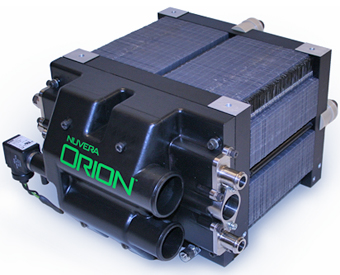
Getting Rid of Platinum
The big R&D driver for PEMFC fuel cells is the automotive industry. Hydrogen fuel cell vehicles are expected to play an important role in reducing greenhouse gas emissions and meeting 2020 emission standards in the U.S. For example, preparation, California plans to spend about $18 million to expand its network of hydrogen fueling stations across the state, with the goal of supporting one million zero-emission vehicles by 2020. To make this happen, though, fuel cell-powered cars must be affordable, which means getting rid of platinum.
Large amounts of platinum are required for PEMFC electrodes to achieve necessary conversion rates. “However, using expensive platinum as a catalyst for the oxygen reduction reaction results in high fuel-cell cost,” said Partha P. Mukherjee, assistant professor of mechanical engineering at Texas A&M University.
One way to reduce platinum content is by developing platinum alloys that are just as effective as platinum, but contain much smaller concentrations of the metal.
“Very low-platinum electrodes are being fine-tuned by some suppliers to ensure both performance and durability,” indicated Scott Blanchet, director of technology development for Nuvera Fuel Cells, a developer of fuel cell technology. “For example, Nuvera successfully completed a DOE-funded program in 2012 that demonstrated 12.5W per milligram of platinum in a full-format fuel-cell stack. Today’s ultra-low-emission gasoline passenger vehicles contain about 10 grams of platinum-group metals in their catalytic converters. So, at 12.5W/mg, a 125-kW fuel cell would contain the same amount of platinum as a typical gasoline car on the road today, but produce no carbon emissions.”
European scientists have developed an electrode material that uses only 10 percent of the amount of platinum that is normally required. The researchers discovered the efficiency of the nanometer-sized catalyst particles is greatly impacted by their geometric shape and atomic structure. Instead of being round, the platinum-nickel alloy nanoparticles are octahedral-shaped, which accelerates the chemical reaction between hydrogen and oxygen.
Another new catalyst has been announced at the University of Wisconsin. There, researchers have deposited nanostructures of molybdenum disulfide on a disk of graphite, which was then subjected to a lithium treatment to create a unique structure with improved catalytic properties. Also, in June 2013, UK-based fuel cell developer ACAL achieved a run time of 10,000 hours for a fuel cell without any significant signs of degradation. Unlike a conventional PEMFC, ACAL’s technology utilizes a liquid catalyst that acts as both a coolant and catalyst, eliminating the need for platinum.
On the Horizon
The fuel-cell industry continues to gain strength. Successful fuel-cell deployment has been demonstrated in key economic regions of the world, such as Korea and California. However, a major breakthrough in electrode chemistry and performance must be made to create widespread market demand.
"Platinum is so expensive [about $4,000 per fuel-cell car], and such a limited resource, that we must find a way to replace it if fuel-cell cars are going to succeed,” said Zhongwei Chen, professor of engineering at the University of Waterloo in Canada, who is working with U.S. Department of Energy to develop nonprecious materials to replace the platinum catalysts in fuel cells.
"Here at Waterloo we are using nanotechnology to create advanced non-precious alternatives for platinum that are a fraction of the cost of platinum, yet provide comparable durability," Chen added. "If we can find a suitable alternative to platinum, it could help pave the way for the motor industry to adopt hydrogen fuel cells for more than a million new vehicles by the end of the decade."
0 comments:
Post a Comment